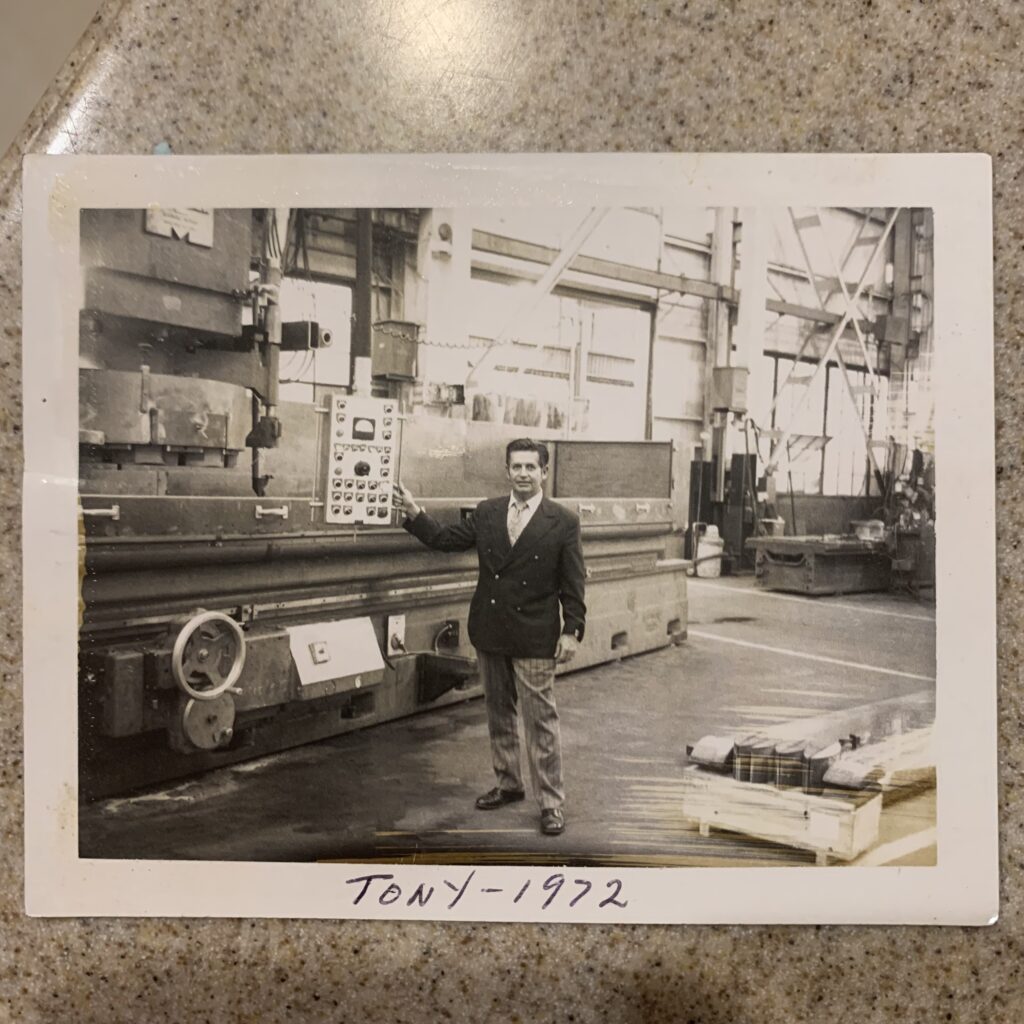
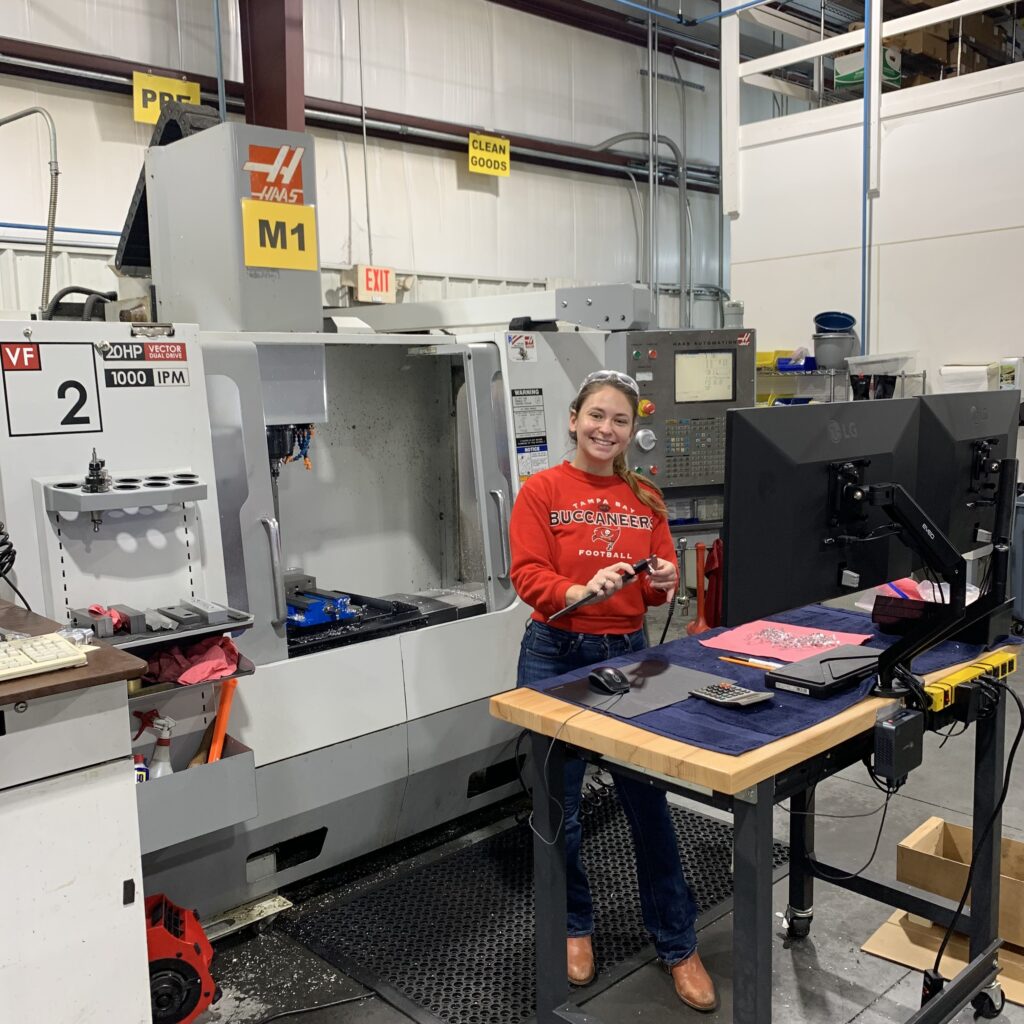
LOCAL MACHINE SHOP AND ENGINEER MUTUALLY BENEFIT FROM DIVERSE EXPERTISE
From Resume:
- Performed setup and teardown of work orders on Haas CNC mill and lathes, including tool prep, touch off, and breakdown
- Machined and recorded metrology analysis on production level parts for final shipment of work order to customers
More Information:
“The mentoring that I received from Sam intrigued me to learn more and continue pushing the boundary of my knowledge beyond what I had learned in undergraduate studies.”
I began working at Catamount as a part time job to extend my reach of learning in 2019. The scope of my learning objectives are to fully understand the manufacturing process, from the moment the purchase order is initiated, until final delivery of the product – and what it really takes to put a machined part into production. When I first started working with Catamount as a client on the engineering side, my foreman, Sam Hytovick, provided helpful feedback on my drawings as to what was possible, plausible, and what made the parts that I designed simpler and faster to machine. The mentoring that I received from Sam intrigued me to learn more and continue pushing the boundary of my knowledge beyond what I had learned in undergraduate studies. I am thankful for them welcoming me onto the team and am enjoying my “shop time” with them on the weekends. In turn, the machine shop benefits from another trained pair of eyes that perform in-depth quality analysis of the machined parts, and consistent work on weekends to buffer what is left incomplete during the work week.
I have learned how to set up, operate, and teardown a machine, as well as assemble various client assemblies. Working at the machine shop requires me to constantly analyze other’s engineering drawings and perform quality inspections of the parts that come out of the machines. This has been helpful for building on my manufacturing skill set that I use on a daily basis at MicroMaterials, and have used in my previous places of employment. I hope to continue building on the skill set by continuously practicing G code in regular operation, learning how to completely translate an engineering drawing (.dwg) file into a G code program, and programming the operation of FANUC automated robots.