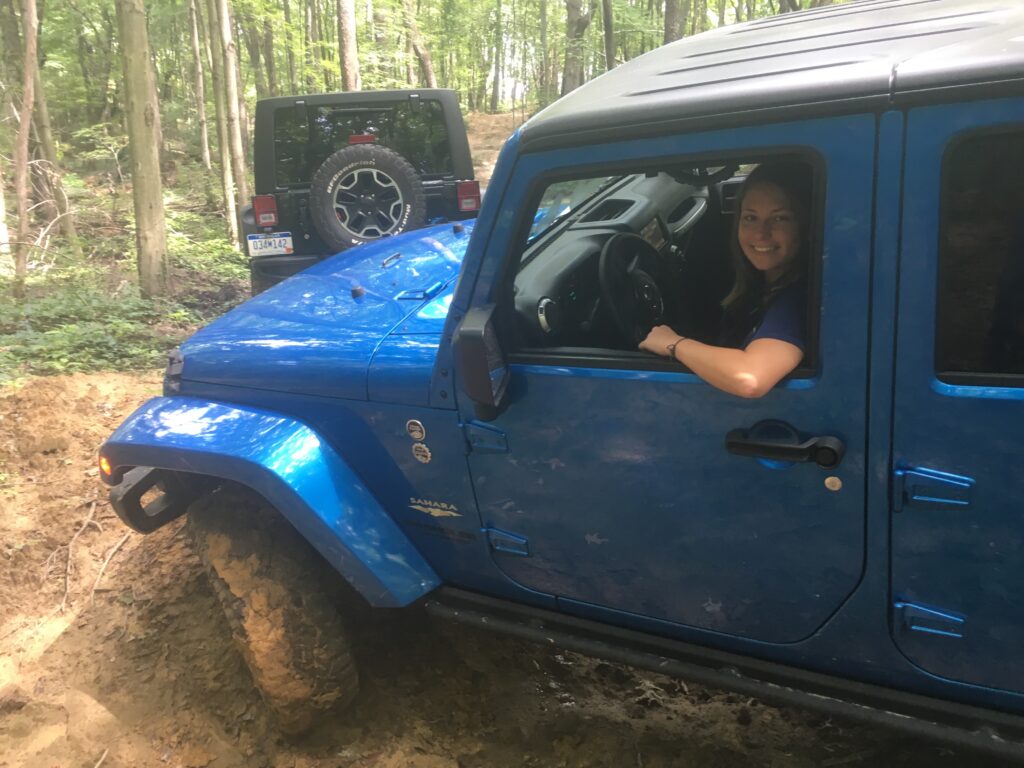
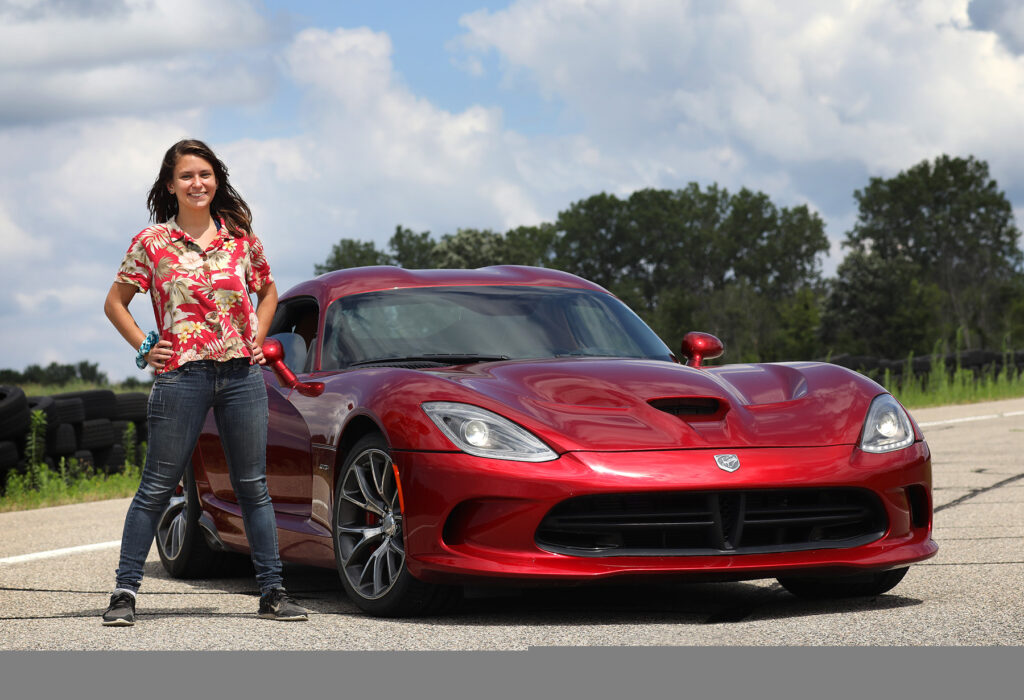
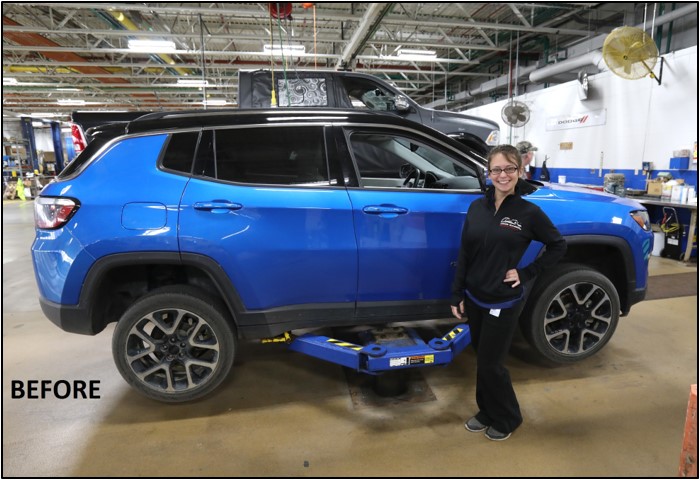
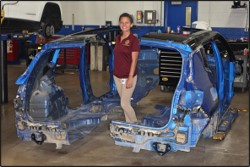
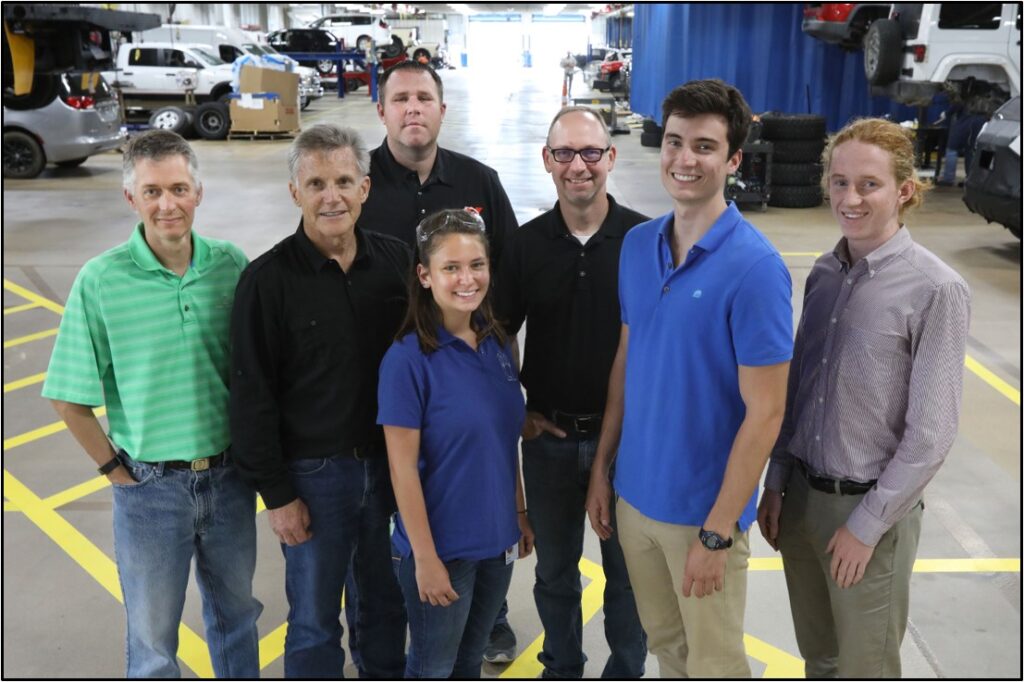
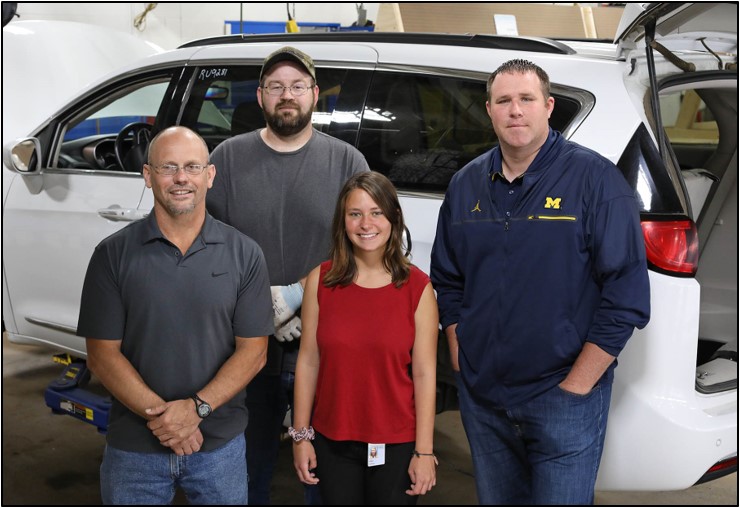
Pictured: Rachael Rosko and Chelsea Proving Grounds (CPG) Durability Quality Group
“FIAT CHRYSLER (FCA) IMPLEMENTS NEW TEARDOWN PROCESS THAT WILL SAVE MONEY IN DURABILITY RELATED WARRANTY COSTS THROUGH PREDICTIVE MEASURES”
From Resume:
- Durability Quality Intern, Chelsea Proving Grounds, Chelsea, MI
- May-August 2017
- Launched pilot program to expand quality insight for post-durability-test vehicle teardown from car to metal frame base
- Fiat Chrysler adopted program for global incorporation in quality verification process to reduce warranty costs
More Information:
Background/Issue
Therefore, the scope of my project was to uncover additional issues with the cars that couldn’t be seen in the first 100,000 miles of durability testing. This would allow the team to give additional feedback to the engineering design team and thus improve quality of the cars.
The FCA Chelsea Proving Grounds (CPG) is responsible for durability assurance of all Fiat Chrysler models as they come off the assembly line. Through regular durability testing up to 100,000 miles, they are able to test and give feedback to the respective engineering design teams at the company for quality assurance as well as provide information on the failure mode and at what mileage certain components will begin to perform differently from the original installation. One thing these tests tend to overlook is what will happen to the car in the following 100,000 miles. Therefore, the scope of my project was to uncover additional issues with the cars that couldn’t be seen in the first 100,000 miles of durability testing. This would allow the team to give additional feedback to the engineering design team and thus improve quality of the cars.
A complete vehicle teardown was performed on one Jeep Compass (MP) and a Chrysler Pacifica (RU). The hypothesis was that CPG could do six teardowns per year and that not too many issues would be found on the RU and MP, as they are PS level cars, or very well built cars with little known functionality issues during testing. These were chosen so the process could be developed and the crew could get their feet wet.
Solution
I was responsible for the process implementation at FCA CPG. The scope of the project was complete teardown of two vehicles that completed the durability test to saleable assemblies such as Body in White (BIW), Body On Frame (BOF), transmission, and engine.
FCA implemented a global end-of-test vehicle teardown in each of its proving grounds in Arizona, Michigan, and FCA Latin America (LATAM) branches. I was responsible for the process implementation at FCA CPG. The scope of the project was complete teardown of two vehicles that completed the durability test to saleable assemblies such as Body in White (BIW), Body On Frame (BOF), transmission, and engine. The hypothesis was that we would uncover issues that cannot be seen while the vehicle is on test and issues that may not cause functionality issues immediately but will in the future. The created process includes instructions and aid for Chelsea Proving Grounds at a system level.
Result
The findings from the study came up with 30 new issues between the two vehicles, 3 of which root cause analysis was performed and verified.
The findings from the study came up with 30 new issues between the two vehicles, 3 of which root cause analysis was performed and verified. The next steps by the time I completed my internship were to continue working with the LATAM and AZ branches to perform further vehicle teardown analysis to related car groups and continue to improve quality through this project.