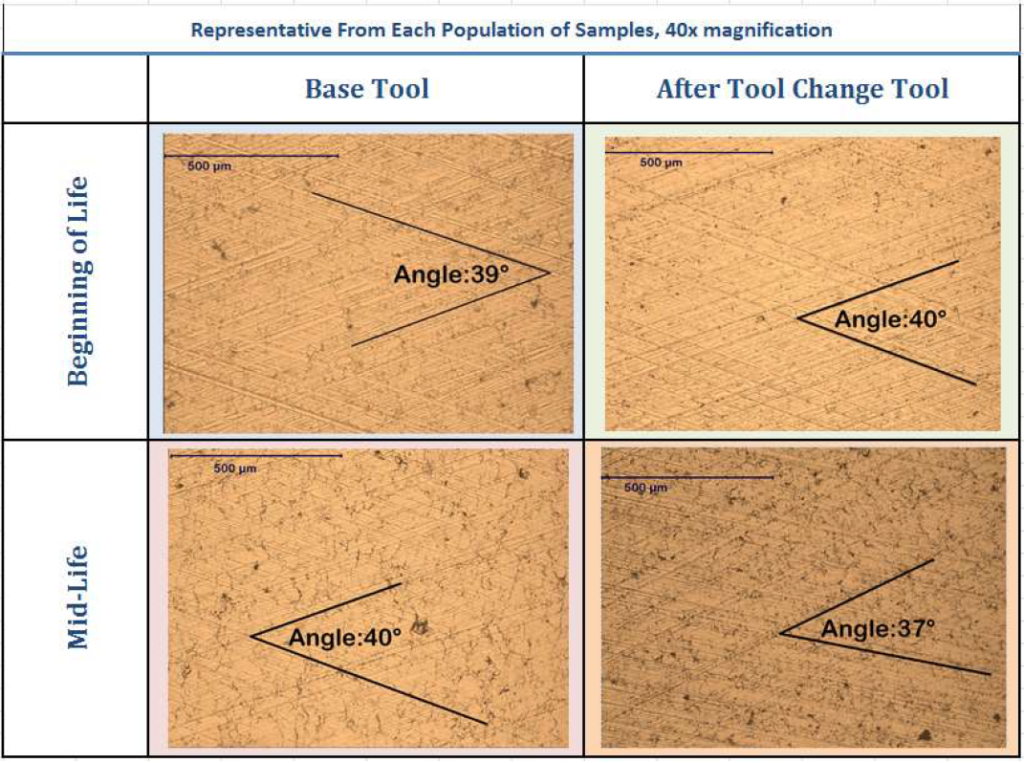
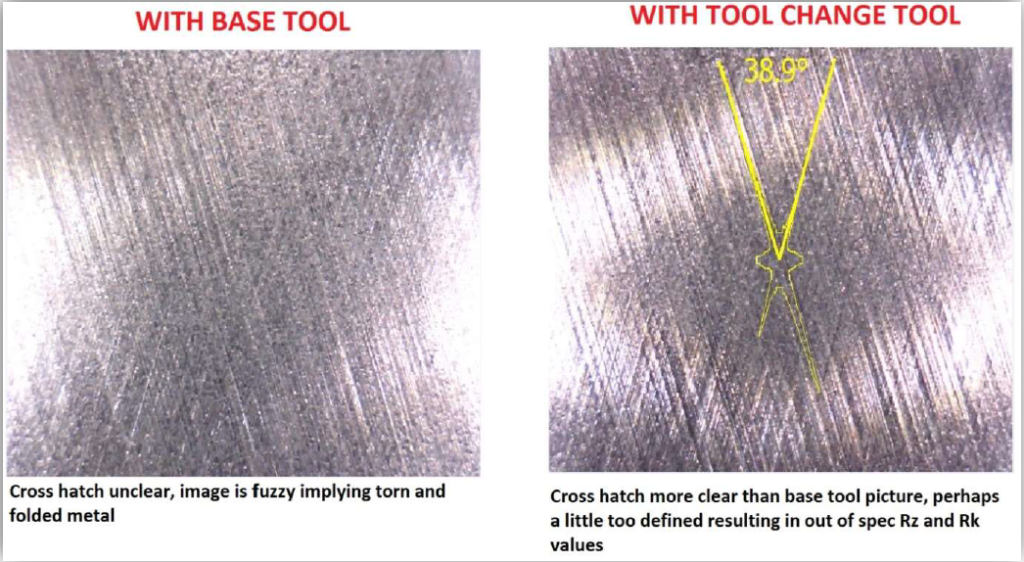
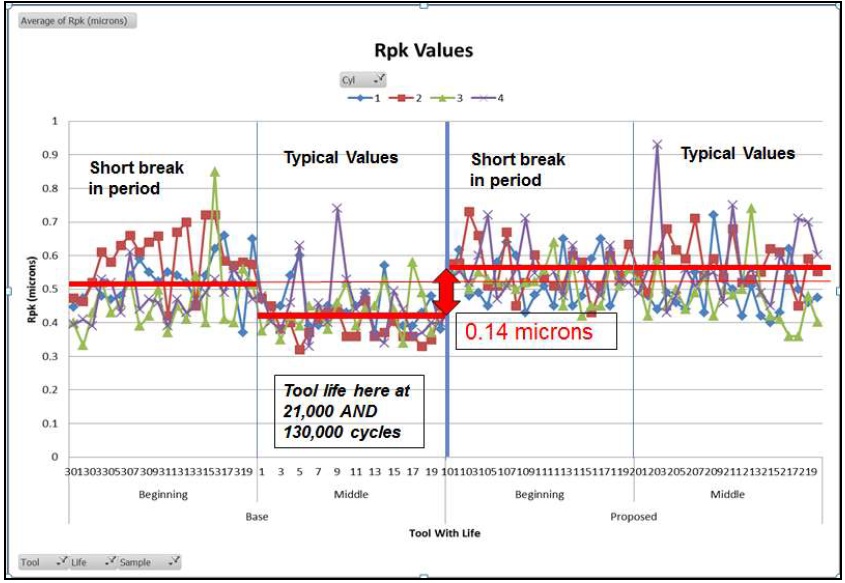
Pictured: Samples of data collected from Cylinder Bore Honing Report
“FIAT CHRYSLER (FCA) ANALYZES SURFACE FINISH OF CYLINDER BORE HONING QUALITY AS POTENTIAL ROOT CAUSE OF EMISSIONS RELATED WARRANTY ISSUES”
From Resume:
- Engine Quality Intern, Dundee Engine Plant, Dundee, MI
- May-August 2016
- Evaluated micro-structural surface finish of cylinder bores in 1.4L engines for torn and folded metal to improve warranty cost and oil consumption by analyzing profilometer readings, fax film, and surface finish Rpk, Rvk, Rk parameters
More Information:
The cylinder bore honing analysis was similar to a university independent study where I worked alone to test, record, and analyze data in a company laboratory at the Dundee Engine Plant in Dundee, Michigan. I worked under several mentors who helped guide me in the education and implementation of this process and I am thankful for their support in this project. (Mentor list and full study are listed in attached document).
Background
The Dundee Engine Plant has known warranty issues with high oil consumption that have not been diagnosed with a known root cause. One possibility lies within the cylinder bore finish and the associated quality. Analysis on cylinder bore finish using profilometer readings, fax film, and microscopic analysis was performed. The results produced showed a trend of better surface finish, clearer crosshatch angles and less smearing with a newer and softer honing stone. However, making this tool change would cost the Dundee plant $187,200 more annually than what we are already paying. Only qualitative data can be drawn from fax film analysis. Further investigation for a cost/benefit analysis must be obtained to make a definitive stance on the argument. The data depicted in this report helps to reinforce cylinder bore surface quality in relation to the hardness of the tool as a likely root cause and gives a more thorough analysis on tool hardness comparison and wear of each tool over time.
Issue
The Tiger Shark Engine has the second highest warranty issues targeted for oil consumption in the company, Dundee Engine Plant being in 3rd for the issue. The piston pack and cylinder bore are two primary parts in the combustion engine that contribute to high oil consumption. On top of that, these cylinder bores have also had continual issues with torn and folded metal. It is predicted that torn and folded metal (TFM) and a non-plateau finish for cylinder bores will cause the piston, as it breaks in around that uneven surface, to begin to wear at an accelerated rate and will also cause the engine to retain less oil. The excess wear at the beginning of the piston packs’ life could potentially cause more chips and gaps in the piston rings or light vertical scratches on the cylinder bore, resulting in excessive pathways for oil to travel through and possibly leading to high oil consumption.
Solution
Part of the solution in diagnosing a root cause to oil consumption required an analysis of cylinder bore honing quality. Fax filming, profilometer reading, and topographical research was done on 20 sample parts (every 15 of 300 parts for both the base tool and the after tool change tool, both at the beginning and middle of each tool’s life) to acquire potential root causes and analyze the cost/benefit to changing the current tools to a softer finish honing tool. It was hypothesized that the softer change tool would wear at a quicker rate than the harder base tool by about 85,000 blocks. This meaning the after change tool is expected to hone 85,000 less blocks than the base tool. Since the base tool is harder, it is predicted that the roughness of the tool is causing the undesired smearing (or TFM) and that changing to a softer tool will allow optimal crosshatch angles and surface quality with less smearing. Because these tools cost approximately the same amount, it is predicted that the after tool change tool will be more costly as it will need to be replaced more often (since it will wear quicker). The wear rate of each tool and the consistency in quality throughout the tools life was also analyzed as a secondary theme. It is predicted that both tools would wear quicker at the beginning of their lives then plateau out to wear at a steadier rate.
Result
The results obtained from this investigation prove the hypothesis correct that the newer softer tool generates better surface finish quality, clearer crosshatch angles, and less smearing. The new tools also, as predicted, wear down at a much quicker rate than the base honing tools and would cost Dundee Engine Plant $64,200 more annually than what they were already paying, or 33 cents more per block. The new honing stones change how quickly they wear over time in that they wear faster at the beginning of the tool’s life than towards the end. Further investigations must be made in order to take a definitive stance on cost/benefit and whether or not this company’s investment to change to the new tool would produce sufficient change. The data depicted in this report helps to reinforce cylinder bore surface quality in relation to the hardness of the tool as a potential root cause, though it is more likely that the bulk oil loss is coming from other sources in the engine such as bore distortion.